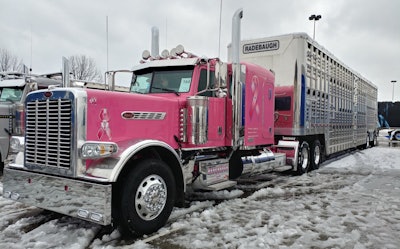
It takes a certain kind of driver to be a livestock hauler. You have to know how to handle your truck and know how to handle the specific livestock you’ll be working with. It’s challenging work, but it comes with its own rewards.
Because of the sensitivity of their freight, whose health can be jeopardized by hours-long stops, livestock haulers have repeatedly been granted ELD exemptions.
“Animal welfare is our big talking point that separates us from other people,” says Allison Rivera, executive director of government affairs for the National Cattlemen’s Beef Association. “You can’t compare hauling toilet paper to hauling live animals.”
Livestock haulers have to run hard and often sacrifice personal convenience to get their freight safely to its destination. They often risk personal injury, such as getting kicked by a cow or stung by bees.
Despite those challenges, livestock haulers say it’s a rewarding field because of the pride they take in their jobs and the responsibility they embrace in caring for the live freight. Being a more specialized field, its compensation is usually equal to or higher than other kinds of driving.
Its specialization has stood out most noticeably in recent months due to the ELD exemptions Congress has provided. The most current one runs at least through Sept. 30, allowing livestock haulers to continue to use paper logs to record duty status. Efforts have been undertaken in recent years to alter hours of service regulations for livestock haulers – and then attempt to bring the segment into compliance with the ELD mandate – as a long-term fix.
One request, filed to the Federal Motor Carrier Safety Administration in February, asks for a 16 hour on-duty period with a 15-hour drive-time window after an off-duty period of 10 consecutive hours. A bill introduced in January in the House would allow drivers hauling livestock and insects expanded hours limits if they stay within a 300-air-mile radius of the source of their loads.
A bill filed in the Senate in March would require FMCSA to establish a committee to recommend ways to reshape hours regulations and ELD requirements for those hauling livestock and agricultural commodities.
HAULING CATTLE
Cattle make up the biggest population of livestock being moved, says Jara Settles, a vice president for the Livestock Marketing Association. There are fat cattle, feed cattle, calves, and other types, each of which can require different handling.
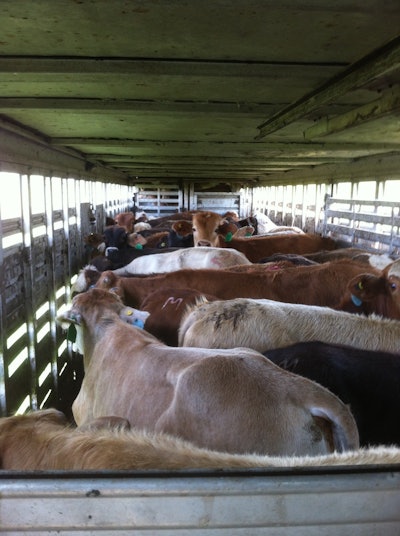
Even the background of the cattle can affect how they behave, says Texas-based owner-operator Zach Beadle, who drives a 1976 Peterbilt cabover. He’s been hauling cattle as an independent since 1989.
Some cattle ranchers “don’t go visit their livestock much,” Beadle says. “They just turn them out and let them be wild. Well, when they round them up, they are as wild as the West Texas land.”
Cattle also can require sensitivity on the part of their transporters when the move is from one temperature extreme to another.
“All of these things have to be taken into consideration,” Rivera says. “You don’t want to be delivering animals that are ill to a feedlot or packing facility.”
It’s usually up to the driver to load and unload the cattle. Some ranches and feedlots have cowboys to help, but that help isn’t always welcome.
“A guy that loads his own truck will be further down the road without trouble because he knows his own trailer, and he’s familiar with what size cattle and how many of what size cattle will fit in a compartment,” Beadle says.
Another challenge is “shrink,” referring to weight loss in transit due to stress or other factors. Excessive shrink can cause a cattle hauler to fall out of favor with a producer. “They know how much cattle should shrink over a given period of time,” Beadle says. “The more they shrink, the less the man makes money.”
Minimizing shrink is one of the factors drivers must consider in how they handle their trucks. Wear and tear on the trailer is another. Sharp braking when hauling cattle could cause some to fall and get injured. A cow could die if it stays down, so drivers may have to go as far as to get into the trailer and try to get the animal propped up. Cattle also can cause damage by bumping into a trailer’s gates or door jambs.
“That’s why livestock trailers are so expensive, and they’re expensive to maintain because livestock are constantly tearing them up.” Citing pricing on new equipment, Beadle says, “You’re not going to touch a well-built rigged-out trailer in the livestock business for less than about $80,000.”
Used road-ready livestock trailers usually run from $35,000 to $50,000. Trailers needing repairs can run as low as $15,000 to $20,000, but the repairs might run as high as $10,000, Beadle says.
As a company driver for VNS Trucking, cattle hauler Shaina Frolik of Rice Lake, Wisconsin, doesn’t have to worry about buying replacement trailers, but she still can be affected by trailer damage.
“If you get a really, really wild cow that busts up your trailer, it’s my responsibility to get it somewhere to get it fixed before my next load,” Frolik says. “So I still get the downtime of it.”
Frolik says her income as a cattle hauler has mirrored what she saw when she hauled flatbed. Beadle agrees that the pay is comparable to other segments of trucking. Most companies pay either mileage or percentage of revenue.
Drivers who want to get into the livestock hauling industry should have prior general livestock handling experience, Beadle says. A driver has to understand the animals and adapt to each load.
HAULING PIGS
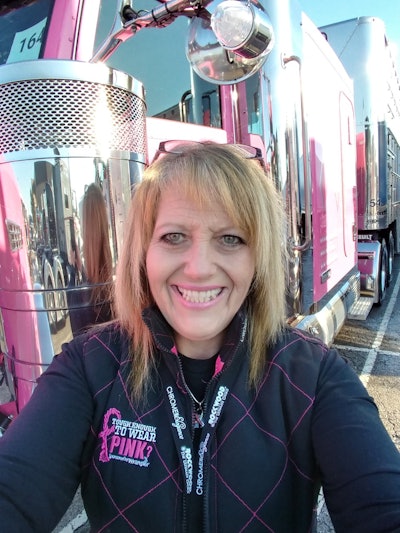
Pamela Cox of Pandora, Ohio, has moved cattle, horses, pigs, sheep, goats, buffalo, and even deer, but she now primarily hauls pigs. She drives for Radebaugh Inc. and has been hauling livestock for 32 years.
Hauling pigs, as well as goats and sheep, generally pays better than cattle, says Cox, in line with the industry saying, “little feet, big money.” However, the market for those animals isn’t as large as the cattle market, she says. Before she settled into her pig run, Cox hauled cattle in Texas.
“Last year, I cleared $52,000 and didn’t work nearly as hard as I have in 27 years in Texas, where I was lucky if I cleared $43,000,” Cox says.
Most producers load and unload their pigs, which takes that pressure off the driver. “It takes longer to load pigs because you can only bring them up in, like, groups of six,” Cox says. “If you’re lucky, you may be able to get 12 to come out.” Sometimes a loader is used to lift the pigs into the trailer.
Pigs struggle to regulate their body temperature, so haulers can’t stop for long during the summer. “Pigs don’t sweat, so you have to keep moving and keep air on them,” Cox says. Likewise, trailers may need boarding up in the winter to keep pigs warm, often more than what cattle would require in a similar situation.
Pigs also differ from cattle in that their behaviors don’t vary so much. Because they are smaller, they are easier on equipment, not trying to kick holes in the trailer like cattle or buffalo will, Cox says. “They will sooner squeal at you and run than kick.”
HAULING BEES
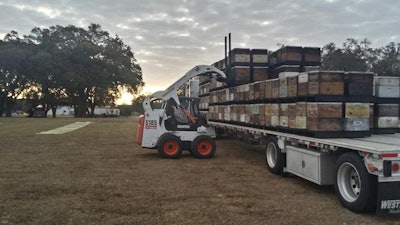
Husband-and-wife team Bud and Aneisha Chapel of Pocatello, Idaho, operate SS Olson LLC, hauling bees with a 2018 Kenworth T680 and a Western 48-foot step-deck trailer. When they started six years ago, they shadowed other bee haulers.
“They trained us a lot, but then we just started watching every load and talking to the beekeepers,” Bud says.
Bees are loaded in boxes containing hives but are free to fly out, so Bud and Aneisha wear protective bee suits while loading and unloading. Once they’re loaded securely, a net is thrown over the bees.
The Chapels always load at sunset because that’s when the bees are calmest. For the same reason, the Chapels fuel only in the morning or at night, making a point not to stop during daylight hours.
During hot weather, bees are loaded to keep the wind directly on them to keep them calm. The Chapels keep a water hose on their truck and water the bees when they park at night. Should the truck stop for a daytime emergency, the hauler also will spray water on them to keep them calm.
If it’s below 20 degrees, they put a small face tarp on the load’s front to block the coldest wind while allowing air to circulate from the sides. When parking in subfreezing temperatures, the Chapels find two reefers or other trucks to park between so the bees don’t get too cold.
“We try to haul specific to the bees’ needs instead of our needs,” Bud says.
Most bee hauling chases the pollination opportunities in certain areas over about nine months, with each haul running two or three days. Demand falls off in July and August because of honey production, so the Chapels usually take time off then. Around February, there’s another slow period because many bees are in California for pollinating.
The Chapels usually run four to 12 weeks at a time. “When the bees are on, the bees are on, and you just don’t go home,” Bud says.
Bud says bee hauling compensation averages out with what the broader trucking industry sees, though with more time off. If customers are willing to pay more for a more experienced bee hauler, pay can be higher, but the slow seasons tend to bring the annual earnings closer to trucking industry averages.